Kostentransparenz im produzierenden Mittelstand
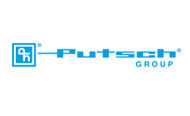
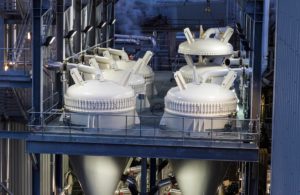
Mit der Betriebsdatenerfassung von top flow sorgt Putsch für Kostentransparenz im Arbeitsprozess.
Nach der Umstellung auf das ERP-System von SAP ging der Maschinen- und Anlagenbauer Putsch den nächsten Schritt, um die Kosten seiner Produktionsprozesse transparenter zu gestalten. In weniger als einem halben Jahr implementierte das Traditionsunternehmen die Betriebsdatenerfassung von top MES und profitiert seitdem von aussagekräftigen Daten für Soll-Ist-Vergleiche.
Weltweit werden jedes Jahr fast 200 Millionen Tonnen Zucker produziert. In einem mehrstufigen Prozess verarbeiten Fabriken und Raffinerien dafür insbesondere Zuckerrüben und Zuckerrohr. Höchst erfolgreich entwickelt und konstruiert die aus dem westfälischen Hagen stammende Putsch GmbH seit über 140 Jahren Maschinen und Anlagen für den globalen Markt. Darüber hinaus plant und realisiert Putsch auch ganze Zuckerfabriken und Zuckerraffinerien. Doch die internationale Führungsposition ist für das Unternehmen eine kontinuierliche Herausforderung.
Projektüberblick
Die Ziele
- Sämtliche Betriebsdaten digital erfassen, sämtliche Prozesse in der Fertigung digital dokumentieren
- Aussagekräftige Kennzahlen gewinnen, um Kosten und Produktionszeiten zu ermitteln und zu analysieren
- Die Basis für weitere Digitalisierungsschritte legen
- Nahtlose Implementierung in kundenspezifische SAP-Umgebung
Die Lösung
- BDE des Manufacturing Execution Systems top MES
- In SAP ERP integriert, keine Schnittstellen erforderlich
- Schrittweise Einführung an allen Fertigungsstandorten
Der Nutzen
- Reduzierter Aufwand durch automatisierte Erfassung, Übertragung und Dokumentation von Betriebsdaten in Echtzeit
- Exakte und konsistente Informationen für Kalkulation und Rentabilität
- Erhöhte Transparenz zu Qualität und Produktivität in der Fertigung
Putsch meistert sie, weil sich das Traditionsunternehmen in allen Bereichen auf Innovationen und höchste Qualitätsstandards fokussiert. „Über den Preis können wir nicht dauerhaft konkurrieren. Aber unsere Anlagen sorgen für extrem effiziente Verarbeitungsprozesse und beste Endprodukte“ sagt Alexandros Georgiou, Leiter der IT-Abteilung. Beispielsweise kann eine hohe Zuckerausbeute nur gesichert werden, wenn die gewaschenen Zuckerrüben vor dem Trocknen von Schneidemaschinen in möglichst exakte, V-förmige Schnitzel geschnitten werden. Schnell und gleichbleibend präzise.
Aufwendige Verteilung von Arbeitskosten
Im Wuppertaler Stammwerk werden Trommelschneidemaschinen, Presskammerfilter für die Feucht-/Flüssigkeitstrennung und andere Maschinen, Anlagen und Werkzeuge gefertigt. Als dort im Jahr 2013 das bisherige Warenwirtschaftssystem vom mächtigeren SAP ERP abgelöst wurde, sollte auch eine digitale Betriebsdatenerfassung (BDE) mit SAP-Standard-Komponenten eingeführt werden, um sämtliche Zeitereignisse zu erfassen. Doch schnell stellte sich heraus, dass die BDE-Buchungen und die Transaktionen über SAP CO19 nicht ausreichend an die Anforderungen von Putsch anzupassen waren.
Zum Beispiel konnte das System keine automatische Erfassung von Mehrmaschinenbuchungen durchführen. Alexandros Georgiou erinnert sich: „Wenn ein Werker parallel an drei Maschinen beschäftigt war, hat er sich an allen drei Maschinen angemeldet und nach vielleicht fünf Stunden Arbeitszeit wieder abgemeldet. In der automatischen Auswertung aber wurden die Maschinenzeiten addiert und ergaben dann unsinnige 15 Stunden Werkerarbeit.“ Um später daraus wenigstens eingeschränkt verwertbare Daten zu erhalten, wurden die Zeiten im ERP händisch nachgetragen.
Zu wenig Einblick in die Produktionsdaten
Hinzu kam, dass die Daten kaum geeignet waren, um eine optimale Maschinenauslastung oder den Materialverbrauch zu ermitteln. Gerade bei der Fertigung von komplexen Maschinen, wenn verschiedene, teils parallele Produktionsvorgänge in ein gemeinsames Produkt münden sollen, entstanden Probleme, falls ein benötigtes Teil noch nicht fertig produziert war. In der Folge ließen sich manche Liefertermine nur mit Mühe einhalten. Denn der Produktion fehlte die Möglichkeit, den Arbeits- und Auftragsfortschritt – beziehungsweise mögliche Fertigungsrückstände – frühzeitig zu ermitteln.
Die Highlights für Putsch
- SAP ERP bleibt das führende System.
- BDE von top MES ist ohne Schnittstellen in SAP integriert.
- top MES bietet anpassbare Dialoge für leichten Einsatz im Shopfloor.
- Controlling, Planung und Vertrieb profitieren von transparenten Ist-Daten.
- top MES ist die Basis für weitere Industrie-4.0-Projekte.
Die mangelnde Transparenz sorgte auch im Controlling von Putsch für wenig Begeisterung: „Ohne reale und verlässliche Werkerzeiten war es unheimlich schwer, die exakten Kosten für die Produktion einer Maschine oder Anlage zu ermitteln. Uns fehlte einfach die Datenbasis für durchgängige Soll-Ist- Vergleiche und zeitnahe Wirtschaftlichkeitsanalysen“, sagt Alexandros Georgiou. Letztlich wirkte sich dieser Mangel auch auf andere Bereiche aus, wie die Planung von Budgets oder eine präzise Kalkulation in Angeboten.
Eine Lösung für den Mittelstand
Ende 2015 war für Putsch der Zeitpunkt gekommen, das Thema grundsätzlicher anzugehen. Das Ziel: Eine BDE-Lösung, die auf Kompromisse – wie sie mit den SAP-Standard-Komponenten notwendig waren – verzichtet. Zugleich sollte SAP als führendes System natürlich erhalten bleiben. „Deshalb konzentrierten wir uns auf Anbieter, deren BDE sich nahtlos in SAP integrieren lässt“, sagt Alexandros Georgiou. Startend im Hagener Stammwerk, wollte Putsch alle Produktionsprozesse über die neue BDE abbilden. Wichtig war dem IT-Leiter und seinen Kollegen eine absolut bedienungsfreundliche Terminaloberfläche. Georgiou: „Wir wussten, dass unsere Transparenzziele nur zu erreichen sind, wenn die Werker gerne mit den Terminals umgehen und keine Bedienfehler dabei machen.“
Schon bald wurden Gespräche mit möglichen Anbietern geführt. Dabei kam die auf top MES aufbauende Betriebsdatenerfassung von top flow auch deshalb in die engste Auswahl, weil sie sich schnittstellenfrei in das SAP ERP integrieren lässt. „Im Kontakt mit top flow hat uns zudem beeindruckt, wie schnell uns die Berater als mittelständisches und zugleich internationales Unternehmen verstanden haben. Nach einem Tag Workshop lag schon ein Pflichtenheft vor – mit passenden Lösungsvorschlägen für unsere speziellen Anforderungen“, sagt Georgiou. Spätestens damit war die Entscheidung für das BDE von top flow gefallen.
Die Mitarbeiter immer eingebunden
Im April 2016 startete Putsch die Implementierung. Die Umsetzung des Pflichtenhefts lief störungsfrei – auch wenn manche individuellen Funktions- oder Dialoganpassungen notwendig waren. Projektleiter Georgiou blickt zufrieden zurück: „Unsere Ansprechpartner bei top flow waren direkt erreichbar und haben das Projekt kreativ vorangetrieben. Damit war das System in Hagen schon nach gut fünf Monaten voll einsatzbereit.“ Zu diesem Zeitpunkt hatten auch die Mitarbeiter ihre Schulungen absolviert. „Wir haben viel Wert auf klare Terminaldialoge und ein für jeden verständliches Userinterface gelegt. Da war der Schulungsaufwand gering.“

Auch bei ihren Filterpressen zur Fest-/Flüssigkeitstrennung verbucht Putsch nun aussagekräftige Betriebsdaten im ERP.
Mögliche Vorbehalte, dass Mitarbeiter nun überwacht würden, hat Putsch schon im Vorfeld zerstreut. Gemeinsam mit dem Betriebsrat informierte man umfassend, wie die BDE funktioniert und welche Daten wozu genutzt werden. Wenn nun ein Werker einen Produktionsauftrag startet, gibt er über das Terminal an der Maschine seine Zeitausweisnummer ein, und was montiert werden soll. Auf die gleiche Weise nimmt das System Unterbrechungen, das Produktionsende oder Rüstzeiten auf und verbucht sie im ERP. So werden über die Zeiterfassung auch die produzierten Mengen und damit der Produktionsfortschritt und der Komponentenverbrauch protokolliert.
„Über die Betriebsdatenerfassung von top MES haben wir jetzt viel mehr Einblick in unsere Kostenverteilung: Werker- und Rüstzeiten, Materialverbrauch oder Produktionsmengen können wir endlich zeitnah erfassen und auswerten.“
Alexandros Georgiou, Leiter der IT-Abteilung bei Putsch
Transparente Kosten zur besseren Kalkulation
Längst ist auch der neue Hauptfertigungsstandort in Wuppertal an das System angebunden. Damit profitiert das Unternehmen auch hier von realen und zuverlässigen Daten aus der Produktion: „Wir analysieren unsere Fertigung nun viel tiefer und exakter als vorher. Den Produktionsfortschritt während eines Auftrags – und die Kosten im Wertschöpfungsprozess“, sagt Alexandros Georgiou. Mit jeder erfassten Produktion wird die Datenbasis noch breiter und aussagekräftiger. Produktionsmengen, Komponentenverbrauch, Zeiteinsatz oder Soll-Ist-Vergleiche werden bei Putsch detailliert ausgewertet und fließen in die Planung mit ein.
Das nutzt auch anderen Bereichen, sagt Georgiou: „Zum einen haben unsere Arbeitsvorbereitung und die Projektteams jetzt Planungsdaten, die für eine optimierte Termintreue sorgen. Zum anderen basiert die Angebotserstellung auf besseren Werten und wir können exakter kalkulieren.“ Entsprechend froh ist der IT-Leiter, dass mit der Betriebsdatenerfassung aus top MES ein erweiterungsfähiges System installiert wurde: „Wir nutzen die Terminals schon jetzt, um den Mitarbeitern Aufspannpläne und andere fertigungsrelevante Dokumente zur Verfügung zu stellen. Und nach und nach wollen wir weitere Produktionsbereiche einbinden.“
Das Unternehmen – Putsch GmbH & Co. KG
- Standort: Hagen (Hauptsitz)
- Portfolio: Planung und Bau von Zuckerfabriken und Zuckerraffinerien
- Gründung: 1871
- Mitarbeiter: ca. 500 weltweit (2018)
- Internet: www.putsch.com
Success Story top MES – Putsch GmbH & Co. KG
Share:
Facebook XING LinkedIn