Predictive Maintenance – Make or Buy?
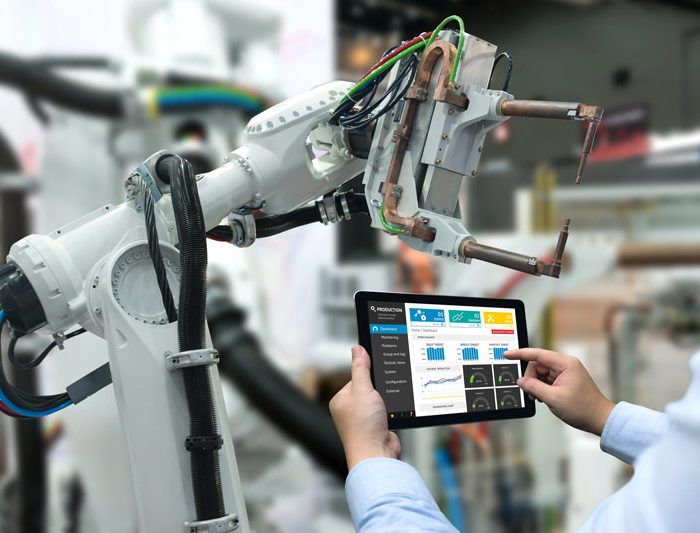
Predictive Maintenance: Unverzichtbar für die Industrie 4.0
Wenn das Konzept Industrie 4.0 an einem konkreten Anwendungsfall veranschaulicht werden soll, wird häufig die vorausschauende Wartung – Predictive Maintenance – beschrieben. Dass gerade dieser Use Case so beliebt ist, hat im Wesentlichen drei Gründe: Erstens ist das Thema für fertigende Unternehmen in allen Branchen relevant. Denn wer Maschinen und Anlagen im Einsatz hat, möchte, dass diese eine möglichst hohe Leistung bringen – und möglichst selten ausfallen. Predictive Maintenance verspricht genau das. Zweitens ist die vorausschauende Wartung kein komplett neuer Gedanke, an den sich die Unternehmen erst gewöhnen müssten. Predictive Maintenance ist lediglich die Fortführung der zustandsabhängigen Instandhaltung oder des Condition Monitorings. Und drittens sind die erforderlichen Technologien einigermaßen etabliert. Betriebsdaten und Maschinendaten können schon seit Jahren digital erfasst werden. Datenbanken, die auf den Umgang mit großen Datenmengen in Echtzeit ausgelegt sind, stehen zur Verfügung. Ebenso Algorithmen, die aus den vielen Daten Prognosen ableiten können.
Welche Bedeutung Predictive Maintenance im Indudie-4.0-Kontext hat, betonte die auf der diesjährigen Hannover Messe vorgestellte Studie „Predictive Maintenance – Service der Zukunft – und wo er wirklich steht“, die vom VDMA und von der Deutschen Messe initiiert und von Roland Berger durchgeführt wurde. Die Autoren arbeiten darin als ein zentrales Ergebnis heraus, dass Predictive Maintenance ein Schlüsselthema für die produzierende Industrie ist. Befragt wurden allerdings lediglich Maschinen- und Anlagenbauer aus unterschiedlichen Segmenten. Die Anwender dagegen nicht.
WEBINAR
Transparente Produktionsprozesse etablieren
Erfahren Sie, wie Sie mehr Transparenz in Ihre Produktion bringen und Optimierungspotentiale aufdecken.
Jetzt zum Webinar anmelden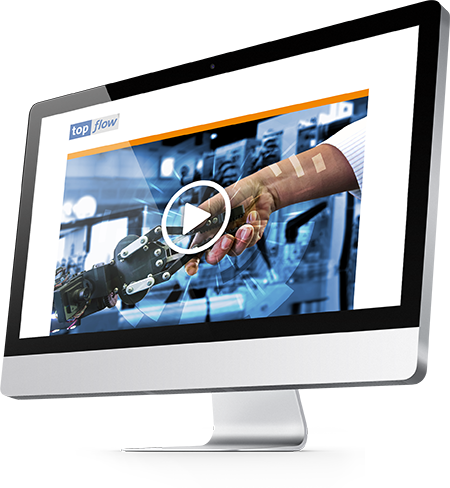
Predictive Maintenance – relevant, aber selten
Bemerkenswert ist eine Beobachtung: Obwohl der vorausschauenden Wartung eine so hohe Relevanz zugeschrieben wird und obwohl für die Realisierung des Konzepts die besten Voraussetzungen bestehen, ist es bislang nur selten Wirklichkeit. So gaben von den für die Studie befragten Maschinen- und Anlagenbauern nur 11 Prozent an, bereits ein vollumfängliches Angebot am Markt zu haben, bei 30 Prozent ist zumindest ein Basisangebot vorhanden. 40 Prozent befinden sich in der Entwicklung. Und 19 Prozent haben noch gar nicht begonnen. Für die Situation bei den Anwendern liegen vergleichbare Zahlen zwar nicht vor. Vieles spricht aber dafür, dass Predictive Maintenance hier noch eine echte Rarität ist.
Strategische Frage: Make or Buy?
Zum einen liegt das am eben noch nicht besonders üppigen Angebot der Maschinen- und Anlagenbauer. Zum anderen stehen die fertigenden Unternehmen vor der strategischen Frage, wie sie die vorausschauende Wartung organisieren sollen. Grundsätzlich gibt es dabei zwei Möglichkeiten:
Buy: Die Unternehmen verlassen sich auf die Maschinen- und Anlagebauer und kaufen Predictive Maintenace als End-to-End-Service mit ein. Vorteilhaft ist dabei, dass sie sich um die Datenerfassung und -auswertung nicht oder kaum kümmern müssen. Da in keiner Werkhalle aber nur Maschinen von einem Hersteller stehen, müssen die Unternehmen dann mit einer Mehrzahl an Services umgehen. Das bedeutet auch, dass die verantwortlichen Produktionsleiter mehrere Service-Dashboards im Blick behalten müssen. Und mehr noch: Bei dieser herstellerorientierten Sicht lassen sich Interdependenzen zwischen Maschinen nur schwer berücksichtigen. Gerade für die Planung von Wartungen ist das aber unverzichtbar. Ein weiterer Nachteil: Solche End-to-End-Services sind für Modelle von morgen oder übermorgen möglich. Maschinen und Anlagen, die aber schon seit einiger Zeit im Einsatz sind und noch ein paar Jahre laufen sollen, bleiben außen vor.
Make: Die fertigenden Unternehmen sorgen selbst für einen Predictive-Analytics-Ansatz, in den sie alle Maschinen und Anlagen – ganz gleich von welchem Anbieter und wie alt – integrieren. Damit hätten sie dann einen vollständigen Überblick und könnten sämtliche Abhängigkeiten berücksichtigen. Der technologische Aufwand ist in diesem Fall jedoch um einiges größer. Und das gilt vor allem deshalb, weil viele fertigende Unternehmen – trotz Industrie 4.0 als Dauerthema – bei der Digitalisierung noch nicht besonders weit sind. So zum Beispiel bei der eigentlich elementaren Erfassung von Betriebs- und Maschinendaten. Papier und Excel-Listen sind nach wie vor weit verbreitet. Die Verbreitung von Manufacturing-Execution-Systemen hat in den letzten Jahren zwar zugenommen, ist aber noch längst kein Standard.
Wer zögert, verliert
Damit Unternehmen fundiert entscheiden können, welcher für sie der richtige Weg ist, sollten sie zunächst die aktuelle Situation in der Werkhalle genau analysieren. Eine Reihe von Fragen zu beantworten, ist dabei hilfreich:
- Welche Maschinen und Anlagen sind vorhanden und welche Daten liefern sie?
- Welche Maschinen und Anlagen müssen in absehbarerer Zeit ersetzt werden?
- Können Maschinen und Anlagen, die bereits älter sind, aber noch weiter genutzt werden sollen, mit Sensorik nachgerüstet werden – um die erforderlichen Daten zu generieren?
- Welche Hersteller bieten welche Predictive-Analytics-Angebote bereits an, wie sehen sie aus und was kosten sie?
- Welche herstellerunabhängige Prognosesoftware ist verfügbar und wie lässt sich diese in die bestehende Infrastruktur einbinden?
Sollte sich bei dieser Bestandsaufnahme herausstellen, dass ein bedeutender Teil der Maschinen und Anlagen künftig über einen End-to-End-Service gewartet werden kann – und das im besten Fall bei nur zwei oder drei Herstellern –, liegt eine Buy-Strategie nahe. Heute dürfte das aber noch eine absolute Ausnahme sein. Deshalb erst einmal nichts zu tun und auf eine zunehmende Standardisierung zu hoffen, ist aber definitiv nicht die richtige Entscheidung. Denn zu schnell kann das zu Wettbewerbsnachteilen führen, die später schwer zu kompensieren sind.
Sinnvoller ist, zunächst einmal die vorhandenen Daten konsequent zu erfassen und über ein Manufacturing-Execution-System zu verarbeiten. Denn damit lassen sich zum einen aussagekräftige Kennzahlen zur aktuellen Situation gewinnen – was ein erheblicher Nutzen ist. Zum anderen kann ausgehend von einer solchen soliden Datenbasis die Wartung sukzessive auf- und ausgebaut werden. Denn fest steht: Bei vielen Unternehmen ist heute noch nicht einmal die zustandsabhängige Instandhaltung oder das Condition Monitoring realisiert. Diese Konzepte umzusetzen, ist also ein erster notwendiger Schritt. Für einzelne Maschinen – vielleicht auch für ganze Fertigungslinien – können dann in Leuchtturmprojekten Prognoseverfahren erprobt werden. Die Erfahrungen werden gesammelt, um damit die passende Strategie immer genauer zu bestimmen. Denkbar sind dabei auch hybride Ansätze: Einige Maschinen sind dann zwar in den End-to-End-Service eines Herstellers eingebunden. Der analysiert aber lediglich die Daten und sendet die Ergebnisse zurück an das Unternehmen. Das kann diese dann mit den Ergebnissen aus anderen Quellen kombinieren. So entsteht der gewünschte Gesamtüberblick.
Dieses Thema könnte Sie auch interessieren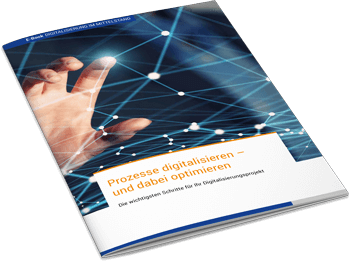
E-Book: So machen Sie Ihre Prozesse fit für die Digitalisierung
Im E-Book „Prozesse digitalisieren – und dabei optimieren“ lesen Sie, wie Sie die bisherigen Prozesse auf den Prüfstand stellen und verbessern.
Artikel teilen:
Facebook XING LinkedIn