Kennzahlen in der Produktion: Die OEE als Königsindikator
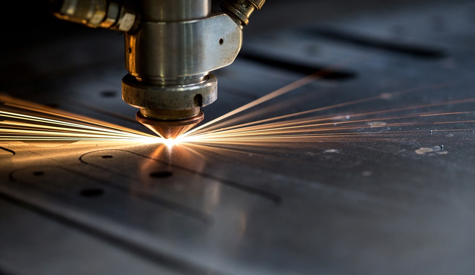
Die OEE ist die wichtigste Kennzahl in der Produktion und damit ein Königsindikator.
Werden Daten im Shopfloor erfasst und systematisch zu Kennzahlen verdichtet – im besten Fall automatisiert mit einem Manufacturing Execution System (MES) –, gewinnen Unternehmen wertvolle Erkenntnisse. Richtig genutzt tragen Kennzahlen dazu bei, die Leistung der Produktion kontinuierlich zu verbessern. Unter den Key Performance Indicators (KPIs) nimmt die in den 1980er-Jahren am Japan Institute for Plant Maintenance (JIPM) entwickelte Overall Equipment Effectiveness OEE; dt. Gesamtanlageneffektivität) eine besondere Stellung ein. Denn die OEE führt alle Faktoren zusammen, die die Performance von Maschine und Anlagen – oder sogar Produktionslinien – bestimmen: die Verfügbarkeit, die Leistung und die Qualität. Auf diese Weise wird nachvollziehbar, wie gut ein Equipment das vorhandene Potenzial ausschöpft und wo Verluste entstehen.
Verfügbarkeit: Wann produziert eine Maschine?
Die Verfügbarkeit gibt das Verhältnis zwischen der möglichen und der tatsächlichen Laufzeit einer Maschine an:
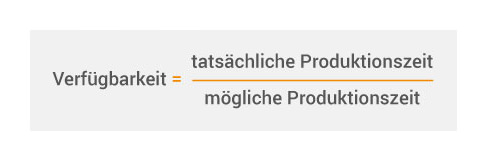
Die Verfügbarkeit ist ein wichtiger Teil der OEE und gibt das Verhältnis zwischen der möglichen und der tatsächlichen Laufzeit einer Maschine an.
Um die Verfügbarkeit für die OEE zu berechnen, muss zunächst die mögliche Produktionszeit definiert werden. Denn nur sehr theoretisch steht eine Maschine 24 Stunden am Tag für die Produktion bereit, Stillstand ist immer wieder geplant. So arbeiten nicht alle Unternehmen im Drei-Schicht-Betrieb samt Wochenende, sondern eventuell nur 16 Stunden an fünf Tagen. Maschinen und Anlagen müssen zudem immer wieder gewartet werden.
Beispiel: Ein Unternehmen arbeitet in zwei Acht-Stunden-Schichten täglich, für die Wartung einer CNC-Fräse sind während dieser Zeit zwei Stunden geplant. Also könnte die Maschine theoretisch 14 Stunden laufen. Tatsächlich läuft sie aber nur 12 Stunden. Die Verfügbarkeit liegt damit bei etwa 86 Prozent.
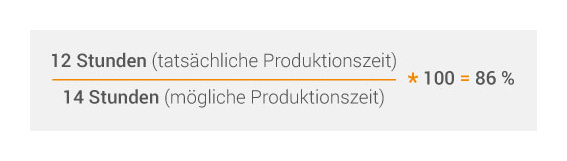
Mit der Produktionszeit kann die Verfügbarkeit einer Maschine berechnet werden. Sie ist damit Grundlage für die OEE.
Für das Unternehmen stellt sich damit die Frage, weshalb die Maschine zwei Stunden lang nicht produzieren konnte, woher dieser Verfügbarkeitsverlust stammt. Drei Ursachen für einen solchen ungeplanten Stillstand sind typisch:
- An der Maschine selbst ist es zu einer Störung gekommen.
- Die Wartung hat länger gedauert, als eigentlich geplant war.
- Es hat an Aufträgen, Material und/oder an Mitarbeitern gefehlt, um die Produktion fortzusetzen.
Je detaillierter Unternehmen die Gründe für einen Stillstand erfassen – kombiniert mit dessen Dauer –, desto aussagekräftigere Schlüsse lassen sich ziehen und umso gezielter können Maßnahmen zur Verbesserung eingeleitet werden.
WEBINAR
Transparente Produktionsprozesse etablieren
Erfahren Sie, wie Sie mehr Transparenz in Ihre Produktion bringen und Optimierungspotentiale aufdecken.
Jetzt zum Webinar anmelden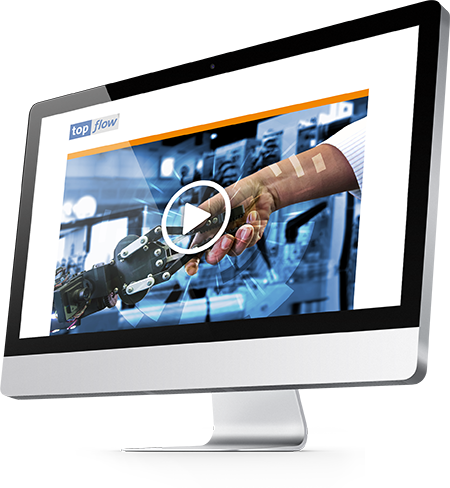
Leistung: Wie schnell produziert eine Maschine?
Auch wenn eine Maschine läuft – also grundsätzlich verfügbar ist –, kann sie in unterschiedlicher Geschwindigkeit produzieren. Und das wirkt sich unmittelbar auf die gefertigte Stückzahl und somit die OEE aus. Die Leistung einer Maschine wird deshalb über das Verhältnis von möglicher zu tatsächlicher Ausbringung bestimmt:
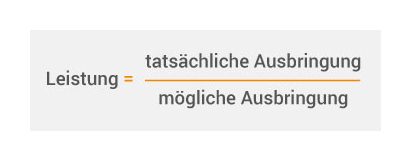
Die Leistung einer Maschine berechnet sich über das Verhältnis der tatsächlichen zur möglichen Ausbringung.
Vor der Berechnung muss auch hier zunächst wieder eine Definition erfolgen. Die Unternehmen müssen bestimmen, wie viel Zeit die Fertigung einer bestimmten Produktmenge im Optimalfall in Anspruch nimmt. Das ist anspruchsvoll, weil die Hersteller zwar häufig Angaben über die Leistungsfähigkeit ihrer Maschinen und Anlagen machen. Da die zu fertigenden Produkte aber sehr unterschiedlich sind, können diese pauschalen Einschätzungen lediglich Näherungswerte sein. Ein pragmatischer Ansatz ist es, die gemessenen Ist-Werte zu verwenden, um den Soll-Wert zu definieren und kontinuierlich anzupassen. Der Soll-Wert sollte also der für ein bestimmtes Stück beste gemessene Ist-Wert sein.
Beispiel: Das Unternehmen hat über erfasste Daten herausgefunden, dass es im besten Fall eine Minute dauert, eine Metallverkleidung auf der CNC-Fräse zu bearbeiten. Pro Stunde könnten also 60 Stücke gefertigt werden. Tatsächlich werden aber nur 45 Stücke gefräst. Die Leistung liegt damit bei genau 75 Prozent.
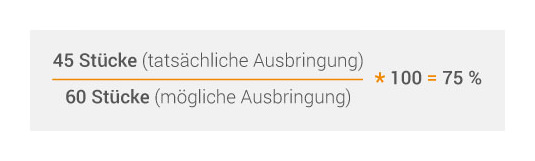
Exemplarische Berechnung der Leistung einer Maschine.
- Während der Produktion ist es an der Maschine immer wieder zu kleineren Störungen gekommen.
- Die Maschine ist nicht in der höchsten Geschwindigkeit gelaufen.
Darüber hinaus sind Abweichungen in der Leistung – positiv oder negativ – oftmals wichtige Hinweise auf fehlerhafte, also zu niedrige oder zu hohe, Soll-Werte. Diese müssen wie oben beschrieben realistisch angesetzt und unter Umständen regelmäßig angepasst werden.
Qualität: Wie gut produziert eine Maschine?
Jeder Arbeitsschritt entlang einer Produktionslinie soll dazu führen, dass Produkte weiterverarbeitet und schließlich verkauft werden können. Insofern kommt es nicht nur darauf an, wie viele Stücke eine Maschine produziert, sondern wie viele davon direkt weiterverwendet werden können. Das Verhältnis dieser beiden Werte gibt die Qualität an, auch sie ein wesentlicher Faktor der OEE:
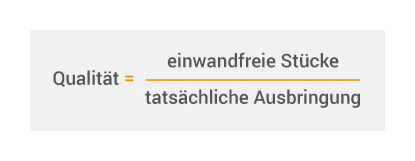
Die Qualität ist ein wesentlicher Faktor der OEE und wird über das Verhältnis der einwandfreien Stücke zur tatsächlichen Ausbringung berechnet.
Da in diesem Fall zwei gemessene Werte in Beziehung gesetzt werden, entfällt für die Unternehmen eine Vorab-Definition.
Beispiel: Von den 45 gefertigten Metallverkleidungen sind zwei Stück Ausschuss, können also gar nicht verwendet werden. Drei Verkleidungen müssen zumindest nachgearbeitet werden. Damit sind von 45 Stücken 40 Stücke einwandfrei. Das entspricht einer Qualität von circa 89 Prozent.
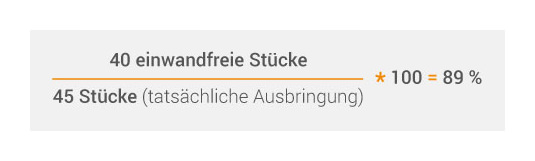
Exemplarische Berechnung der Qualität einer Maschine.
Die möglichen Ursachen für fehlerhafte Stücke sind vielfältig – von Mängeln bei Material und Vorprodukten über Nachlässigkeiten bei den Mitarbeitern in der Werkhalle bis zu Defekten an der Maschine oder Anlage. Um strukturelle Probleme zu erkennen, sollten deshalb die jeweils vorliegenden Gründe für die Qualitätsverluste dokumentiert und mit anderen Gründen ins Verhältnis gesetzt werden: etwa die absolute Anzahl von nicht einwandfreien Stücken pro Ursachentyp, die Häufigkeit der Ursachentypen pro Produkt oder pro Schicht.
Verfügbarkeit x Leistung x Qualität = OEE
Aus der Multiplikation der vorher errechneten Werte ergibt sich die OEE als KPI:
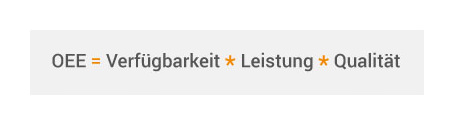
Die OEE ist das Produkt aus Verfügbarkeit, Leistung und Qualität.
Das Unternehmen aus dem Beispiel käme damit also für seine Fräsen auf eine OEE-Kennzahl von etwa 57 Prozent:
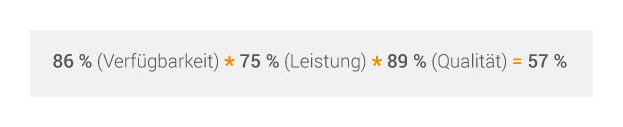
So berechnet sich die OEE aus unserem Beispiel.
Grundsätzlich eignet sich die OEE-Kennzahl zwar zum Vergleich. Stellt man dabei allerdings die absoluten Werte gegenüber, muss sehr genau darauf geachtet werden, dass tatsächlich Vergleichbares miteinander verglichen wird. So ist es beispielsweise, wenn die Gesamtanlageneffektivität einer Maschine im Zeitverlauf betrachtet wird. Ebenso können identische Produktionstechnologien innerhalb einer Abteilung gegenübergestellt werden – vorausgesetzt, Parameter wie Produkt- und Losgrößenmix stimmen überein. Ein rein quantitativer OEE-Vergleich unterschiedlicher Abteilungen oder gar Standorte ist dagegen kritisch.
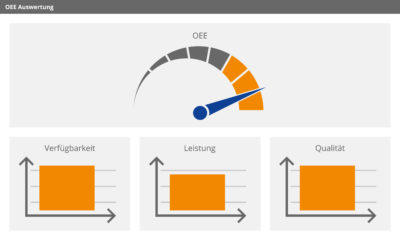
Ist die OEE erst einmal berechnet, bringt deren Auswertung viele brauchbare Ergebnisse.
Kritisch deshalb, weil es vollständig von der spezifischen Situation im Shopfloor und den Rahmenbedingungen abhängt, was ein guter und was ein schlechter OEE-Wert ist. So könnte ein Unternehmen an einem Produktionsstandort eine OEE von 80 Prozent erreichen, an einem anderen von 90 Prozent. Um das richtig beurteilen zu können, ist ein genauer Blick nötig. Beide Standorte produzieren zwar die gleichen Metallverkleidungen. Das 80-Prozent-Werk fertigt aber in kleineren Losgrößen, weil der Markt das verlangt. Hier wurden über die Jahre schon zahlreiche Maßnahmen ergriffen, es ist alles ausgereizt. 80 Prozent sind also hervorragend. Am 90-Prozent-Werk limitiert der Markt die Fertigung nicht. 90 Prozent sind nicht das Optimum, es besteht noch Verbesserungspotenzial.
Ziel sollte es in jedem Fall sein, mithilfe der OEE die Ursachen von Verlusten zu identifizieren und zu beheben. Wichtig ist dabei, immer im Blick zu behalten, dass die drei einzelnen Werte nicht nur mathematisch, sondern auch faktisch miteinander verknüpft sind. Maßnahmen, die auf die Optimierung des einen Wertes abzielen, können sich gegebenenfalls negativ auf einen anderen Wert auswirken. Was bei Zielkonflikten den Vorrang hat, hängt letztlich von der speziellen Situation und der Strategie des Unternehmens ab.
Das könnte Sie außerdem interessieren…
E-Book: So machen Sie Ihre Prozesse fit für die Digitalisierung
Eine Digitalisierung macht Unternehmensprozesse effizienter. Das gilt aber nur, wenn bereits vorher die Abläufe rund laufen. Im E-Book „Prozesse digitalisieren – und dabei optimieren“ lesen Sie, wie Sie die bisherigen Prozesse auf den Prüfstand stellen und verbessern.
Artikel teilen:
Facebook XING LinkedIn