Kramski GmbH – Digitaler Neubau für erfolgreiches Familienunternehmen
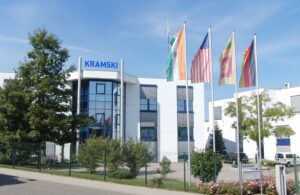
Die Kramski-Gruppe ist stets nah am Kunden: So ist der Spezialist für Stanz- und Hybridteile jederzeit in der Lage, kundenindividuelle Musterkonzepte zu entwerfen und darauf aufbauend Prototypen zu fertigen. Gleichzeitig produziert das Unternehmen aber auf Wunsch auch große Mengen in Serie – etwa für wichtige Branchen wie die Medizintechnik. Ausgangspunkt für die flexible Fertigung ist top MES als zentrales Tool zur Digitalisierung.
Projektüberblick
Das Ziel
- Optimierungspotenziale in der Produktion leichter erkennen und umsetzen durch moderne Dashboards
- Eine verbesserte Produktionssteuerung durch intelligente Datenauswertungen
- Automatisches Verbuchen eingesetzter Materialien
Die Lösung
- Go Live von top MES als neues Manufacturing Execution System und zentrales Tool zur Digitalisierung
- Automatisches Erfassen von Maschinendaten als Grundlage für Dashboards mit wichtigen KPIs sowie zur Ermittlung optimaler Produktionsmengen
- Retrogrades Verbuchen eingesetzter Materialien, um einen besseren Überblick über einzelne Chargen zu behalten
Rund 11 Millionen Menschen in Deutschland leiden offiziell an Diabetes, Typ I und II. Vielen dieser Menschen kann die Medizin helfen, sofern Ärzt*innen die Krankheit frühzeitig diagnostizieren und rechtzeitig therapeutische Maßnahmen einleiten. Neben einer Ernährungsumstellung umfasst dies häufig die regelmäßige Selbstkontrolle des Insulinspiegels. Wichtige Teilkomponenten für die dazu notwendigen Geräte produziert das baden-württembergische Familienunternehmen Kramski. Gegründet 1978 in Pforzheim, ist es mittlerweile an vier Standorten auf drei Kontinenten vertreten, beschäftigt dort insgesamt rund 700 Mitarbeitende und erzielt weltweit einen jährlichen Umsatz von mehr als 100 Millionen Euro. Zu den Abnehmern der Stanz- und Hybridteile gehören namhafte Unternehmen verschiedener Branchen. Doch obgleich die Kunden aus unterschiedlichen Sektoren wie Medizintechnik oder Automobilindustrie kommen, ist ihnen eines gemein: Sie setzen alle auf die hohe Qualität der Kramski-Produkte sowie auf die Fähigkeit des Unternehmens, auch auf individuelle Kundenbedürfnisse einzugehen.
Kein Widerspruch: Individuelle Serienproduktion
Zu den Stärken der Kramski-Gruppe gehört es, stets nah am Kunden zu sein. Das Unternehmen ist so in der Lage, kundenspezifische Musterkonzepte zu entwerfen und darauf aufbauend Prototypen zu fertigen. Es kann aber auch hohe Stückzahlen in Serie produzieren. Derzeit umfasst die Gesamtproduktion mehr als drei Milliarden Teile pro Jahr. Häufig erhält das Unternehmen die Fertigungsaufträge vom Kunden via Electronic Data Interchange (EDI) – und muss darauf zügig reagieren. Selbst einzelne Chargen besitzen dabei oft hohe Produktionsvolumina.
„Für unser Unternehmen ist es daher wichtig, die Produktion notfalls schnell hochfahren zu können, aber dennoch die Ausschussquote möglichst gering zu halten“, berichtet dazu Micha Holzmann, IT-Spezialist bei Kramski. „Dafür ist ein modernes Manufacturing Execution System (MES) hilfreich, mit dem wir beispielsweise die Overall Equipment Effectiveness (OEE) in der Produktion erfassen können. Leider besaßen wir bis vor Kurzem noch kein entsprechendes System für den Live-Betrieb, welches in dieser Hinsicht unsere Erwartungen wirklich erfüllte. Daher verließen wir uns vor allem auf die Erfahrungen altgedienter Mitarbeiter*innen.“
Die Highlights für die Kramski Group
- SAP ERP bleibt das unternehmensweit führende System.
- top MES ist direkt in SAP integriert, neue Schnittstellen sind nicht erforderlich.
- top MES erleichtert das automatische Erfassen von Maschinendaten, ermöglicht so eine KPI-basierte Produktionssteuerung und liefert die Grundlage für Vorschläge zu optimierten Losgrößen.
- top MES erlaubt eine kosteneffizientere Fertigung, indem Daten zur Warnung vor überhöhtem Stromverbrauch genutzt werden. Dadurch trägt es zudem zu Nachhaltigkeitszielen bei.
- Durch ABAP ermöglicht top MES auch künftig einfache Anpassungen
Historisch gewachsene Prozesse durchbrechen
Bis 2018 erfolgten die Produktionsrückmeldungen tatsächlich historisch bedingt nahezu ausschließlich manuell durch die Werker*innen, zunächst via Stechkarten. Anschließend nutzte das Unternehmen ein terminalgebundenes Subsystem, bei dem die Werker*innen Start- und Endzeiten der Schicht sowie Ausschüsse erstmals elektronisch erfassten. Das Unternehmen konnte so schon deutlich schnellere Auswertungen vornehmen, ein vollautomatisiertes, zukunftsfähiges MES bot die Lösung aber nicht. Mit der Lösung war es zudem nicht möglich, systematisch Maschinendaten zu erheben. Daher entschloss sich Kramski, endlich die Grundlage für eine digitalisierte Produktionsplanung- und -steuerung (PPS) zu etablieren, mit der eine OEE-gestützte Optimierung der Produktionsabläufe zukünftig möglich wäre – und das durch eine enge Anbindung an SAP keine neuen Schnittstellen erfordern würde. Nach einer einjährigen Testphase sollte dieses System planmäßig 2021 flächendeckend in Deutschland einsatzbereit sein. Dazu erläutert Nico Axtmann, Digital Production Engineer bei Kramski:
„Uns war klar, dass wir langfristig ein einheitliches System wollten, mit dem sich Daten objektiv erfassen
lassen – und das sich auf unsere spezifischen Bedürfnisse anpassen ließe. Dazu gehörte eine einfache Anbindung an unser SAP-System, aber ebenso die Möglichkeit, Workflows sowie Messpunkte und -größen im Produktionsprozess individuell definieren zu können. In dieser Hinsicht wollten wir nicht länger Kompromisse eingehen, sondern nach einer beständigen Lösung suchen“.
In top flow einen starken Projektpartner gefunden
Bei der Suche nach möglichen Projektpartnern stieß das Unternehmen auf den IT-Spezialisten top flow, der mit dem SAP Add-On top MES eine Lösung anbot, die den Unternehmenswünschen entsprach. Bei top flow handelte es sich dabei um eine alte Bekanntschaft: Schon seit geraumer Zeit nutzte Kramski erfolgreich
top se16XXL als Reporting-Tool – insofern war die Bereitschaft groß, auch für die Einführung des neuen MES einen ersten Kontakt zu dem Softwarespezialisten aus Bad Saulgau aufzunehmen.
Moderne Fertigung durch Industrie 4.0
Das Projekt begann mit einer ersten konzeptionellen Pilotphase, die dem eigentlichen Test- und Produktivbetrieb vorausging und in der das von top flow und Kramski gemeinsam gebildete Projektteam zunächst den grundsätzlichen Aufbau der zukünftigen Lösung skizzierte. Hierzu gehörte beispielsweise die Aufgabenstellung, eine passende Middleware für den Import von Maschinendaten in top MES zu finden. Anschließend implementierte das Projektteam top MES zunächst mit den Standardfunktionalitäten. Diese nutzte das Team als Basis für die kundenspezifischen Anpassungen, die es zunächst in der Stanzerei ausprobierte.
„Dadurch wollten wir vor dem flächendeckenden Rollout sicherstellen, dass unsere Ideen auch in der Praxis funktionieren“, resümiert Nico Axtmann.
Dazu realisierte das Team unter anderem folgende kundenspezifische Anpassungen:
Dashboard mit Key Performance Indikatoren (KPIs)
Für die Messung der Effizienz in wichtigen Teilbereichen implementierte Kramski ein Dashboard mit diversen KPIs. Im Zusammenspiel unterstützen diese Kennzahlen das Unternehmen zudem dabei, übergeordnete Indikatoren wie die OEE leichter zu ermitteln. Zu den auf dem Dashboard hinterlegten Kennzahlen gehören beispielsweise Soll-Ist-Abgleiche bei Rüst- und Belegungszeiten sowie Angaben, wie ausgelastet einzelne Arbeitsplätze sind.
Optimierte Maschinensteuerung durch erhobene Maschinendaten
Die gesammelten und aufbereiteten Maschinendaten werden bei Kramski genutzt, um optimale Produktionsmengen zu bestimmen. Durch die analysierten Daten kann sichergestellt werden, dass Maschinen nicht heißlaufen, sich zu schnell abnutzen oder das Unternehmen durch zu hohen Stromverbrauch kostenineffizient produziert.
Retrograde Verbuchung von Materialien
Durch die vom Projektteam vorgenommenen Anpassungen kann das System wichtige, in der Produktion eingesetzte Materialien, retrograd und automatisch verbuchen. Der Abgleich erfolgt dabei völlig reibungslos – dank der schnittstellenfreien Anbindung von top MES an SAP. Ergänzend implementierte das Projektteam zudem einen automatischen Etikettendruck, der anhand der gemeldeten Mengen funktioniert. Wichtige Informationen zu den Chargen für die Kunden liegen damit immer vor.
Ein stabiles Gerüst für die Zukunft
Dank der gemeinsamen Projektarbeit konnte die Kramski Gruppe den Rollout für alle Arbeitsplätze in Deutschland wie geplant 2021 durchführen. Dem Unternehmen steht somit nun ein zukunftsfähiges MES zur Verfügung, das es aufgrund der leichten Anpassbarkeit via ABAP schnell auf künftige Herausforderungen anpassen kann. Insgesamt erfolgt die Produktion seither deutlich transparenter und effizienter. Neben den Features, die das neue Tool bietet, schwärmt Micha Holzmann auch von der ausgezeichneten Zusammenarbeit zwischen top flow und seinem Unternehmen:
„Die Software ist hervorragend. Sie ist flexibel und einfach zu bedienen. Besonders überrascht bin ich aber von der gemeinsamen Arbeit mit top flow. Ich habe schon in vielen guten Projekten gearbeitet. Aber selten habe ich einen so fairen Partner erlebt. Dazu ein einfaches Beispiel: Bei vielen Softwarelösungen werden individuelle Anpassungen gerne als teure Change Requests abgerechnet. top flow hingegen setzte unsere Wünsche nicht nur zeitnah und kostengünstig um, sondern übernahm einige unserer Ideen sogar in die Default-Funktionen ihrer Software. Das nenne ich konstruktives Teamwork.“
Kramski GmbH
- Standort: Pforzheim (Hauptsitz)
- Portfolio: Stanz- und Hybridteile aus Metall und Kunststoff für Medizin, Mobilität und Industrie
- Umsatz: ca. 106 Mio. Euro (2017)
- Gründung: 1978
- Mitarbeiter: ca. 700 (2019)
- Internet: www.kramski.com
Success Story Kramski GmbH
Artikel teilen:
Facebook XING LinkedIn